Ross Grassick
Forklift Safety
10 Steps to Minimising Forklift Workplace Accidents in Your Warehouse
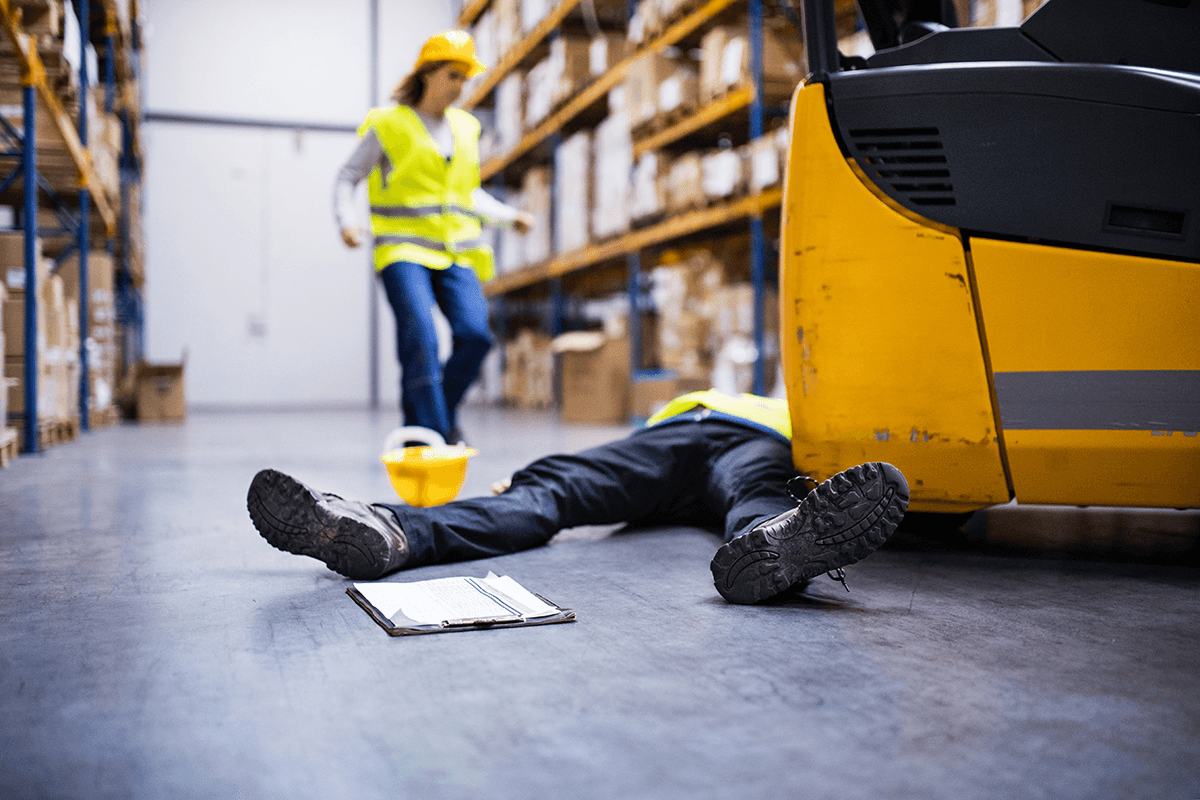
According to Safe Work Australia, there was 3,414 work-related deaths from 2003 to 2016, 190 in 2017, and 118 in 2018. While there’s an obvious improvement, we believe that bringing the figures down relies on educating on the risks associated with forklift use and best practice approaches to forklift safety. We’ve identified 10 steps for you to apply to your workplace to prevent accidents.
1. Train your forklift drivers
Forklifts are dangerous machinery that can cause serious accidents when handled by untrained and inexperienced drivers. It’s Australian law that forklift operators must obtain a valid forklift license through a compulsory training course with a registered training organisation. To be eligible, potential operators must be over 18 years of age.
Trained forklift drivers can improve the efficiency of any warehouse, as their experience will keep workflow going. They’ll know which areas they can operate in to avoid accidents. However, whenever a warehouse floor plan changes, drivers will need to be trained again to ensure they know the new layout.
2. Understand the stability triangle
The stability triangle is resembled in a forklift’s three-point system: the two wheels at the front and the pivot point of the rear axle. For the vehicle to be stable, the centre of gravity and its load must remain within the triangle. If the centre of gravity moves outside of the triangle, the vehicle will be unstable, increasing the risk of tipping over.
All factors that move the centre of gravity relate to the load. A heavier load means the combined centre of gravity will be further forward. Eventually, the forklift load will become heavier than the truck’s rating plate and will move the combined centre of gravity too far forwards and outside the triangle. Loads should be carried as low as possible when moving a loaded truck to minimise the risk for workplace accidents.
3. Implement a pre-start safety checklist
Before an operator uses a forklift, a pre-start safety checklist should be completed at the beginning of each shift and signed off by the supervisor at the end of each week.
This checklist must be completed in an area clear of people and other vehicles. If there are any faults on the forklifts, the supervisor must be notified. The checklist will include:
- Tyres
- Fluids
- Seating
- Warning devices
- Capacity
- Mast
- Hydraulic cylinders and hoses
- Tines
- Guarding
- Controls
- Brakes.
4. Undertake forklift maintenance
Regular forklift upkeep will reduce downtime for forklifts, meaning you can get on with the job without interruptions. Scheduling regular services for your forklift will allow forklifts to run at their peak every time and reduce costs for the warehouse, and any risks identified can be removed once a forklift has been inspected.
5. Keep people away from equipment
Forklifts have warning devices such as horns , strobe lights, and reversing alarms that drivers can use to warn pedestrians. Drivers have to be aware of their surroundings and utilise these features if necessary. You can also have improved visibility with blue lights, which move along the ground to give a clear visual sign that a forklift is approaching.
Hi-visibility vests must be worn at all times, for all staff and pedestrians. There should be no unauthorised persons in the warehouse. It’s best practice to have a sign-in sheet for any visitors and ensure that they’re accompanied at all times.
6. Understand traffic flow
Warehouses have traffic flows that need to be understood by all employees to avoid collisions with pedestrians, stock or other forklifts. Proper marking, signage (such a reflective lines and markers), speed limits, no parking zones, and pedestrian crossings will guide the traffic flow to run smoothly. Any changes to the warehouse layout will affect the traffic flow, and all staff will need to be trained on the new traffic flow.
7. Be cautious of safety slopes and grades
Slopes and grades should always be approached with caution. Drivers will need to ensure they’re a safe distance from the edge of the ramps and that the ramps are wide enough to prevent forklifts from tipping over.
Drivers will also need to know the grade of the incline with the load they’re carrying. Otherwise, they increase the risk of tipping over, causing damage to stock, equipment and injury to the driver.
8. Don’t overload a forklift
As per the stability triangle, you don’t want to overload the forklift as it could tip over and cause major accidents or injuries to pedestrians and forklift drivers. Forklift drivers must understand the load capacity of their forklifts. This information is located on the safety plate attached to the forklifts. It will clearly show the:
- Make, model and serial numbers
- Mast tilt degrees, the forward, rear, up, and down
- Maximum lift height
- Tyre type and pressure
- Gross vehicle mass.
9. Have a well-lit warehouse
Poor lighting increases the risk of accidents and stock damage. On the other hand, having quality lighting in the correct positioning will increase visibility for your forklift drivers and reduce the risk of accidents. The best position to have your lights is over the aisles, since your forklifts will be operating there the majority of the time. There’s an added bonus if your warehouse already has skylights, as the natural light is at no cost to you. Alternatively, state of the art LED lighting would be the way to go due to it having a cleaner light at a lower cost than your standard lighting.
10. Maintain a clean workplace
This may sound obvious, but it can’t be stressed enough how important a clean workspace is. An untidy and cluttered workspace can make the area difficult to manoeuvre with your forklift. Always ensure that rubbish is put in the bin and is regularly emptied to avoid fire hazards. A clean workplace will allow for a reduction of risk when it comes to forklift collisions and workplace injuries.
Contact Lencrow Forklifts for workplace safety advice
For your forklift safety needs, contact Lencrow Forklifts for any advice and one of our experienced team members will help you. Lencrow Forklifts have been an Australian owned family business for more than 40 years. Contact us on 1300 532 276 for all you materials handling needs.