Ross Grassick
Forklift Service & Maintenance
Understanding Forklift Safety and Monitoring Systems
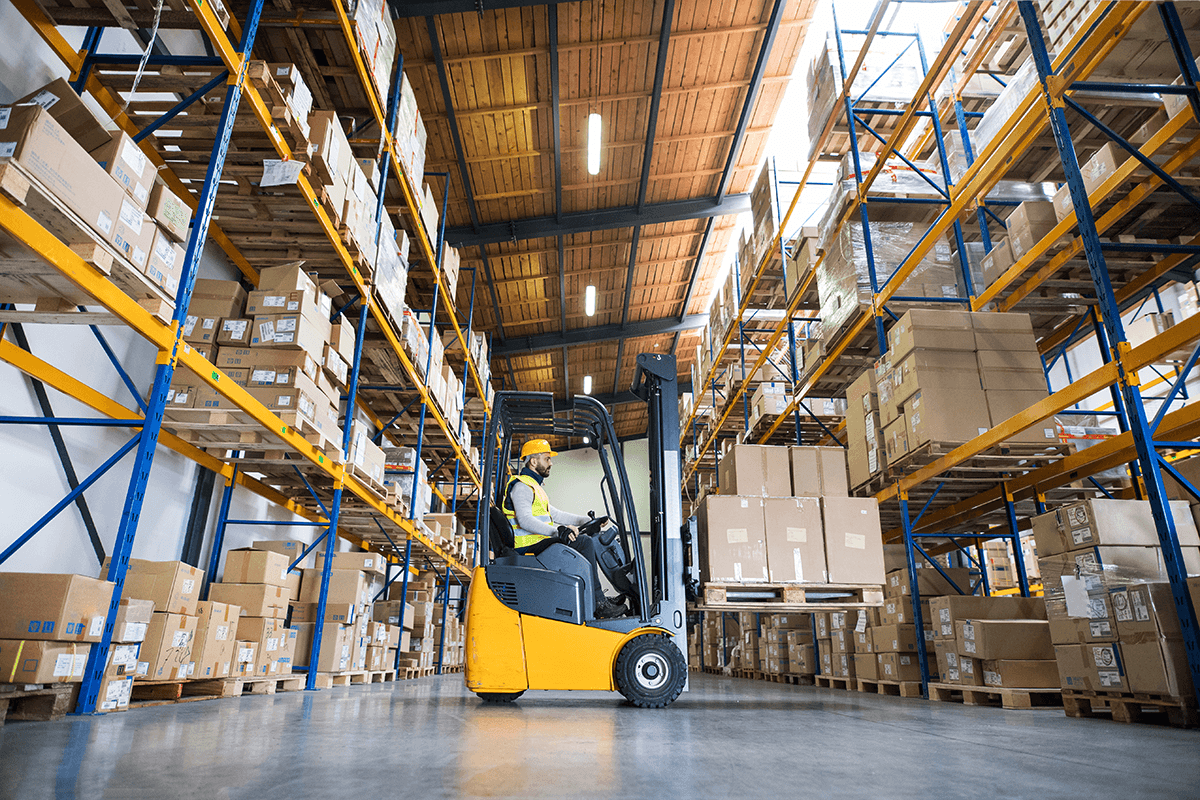
Forklifts have undergone major improvements over the last couple of years due to the introduction of forklift monitoring systems. These systems and safety devices show valuable real-time data to warehouse managers, supervisors and drivers, helping to minimise workplace injuries and damage-related costs. To effectively utilise the safety features, it’s important to understand how they operate and the advantages of them for the business.
What are the benefits of electric forklift monitoring?
Over the years, electric forklift monitoring has gained popularity with fleets, particularly operator present systems. Swipe cards, fobs, and pin entries for driver access control prevent unauthorised persons from using forklifts, reducing the risk of workplace accidents at the hands of an untrained driver. Operator systems make drivers more accountable for their work and therefore increase productivity.
These days, you can have hardware and software products installed in your forklift, such as LCD visual display screens. These can be used for a pre-start-up checklist, and provide drivers with special instructions that they have to complete before each shift to ensure compliance and safety. For most systems, if a driver gives one wrong answer in the pre-start-up checklist then the machine can be locked down, preventing the driver from using the machine.
Different forklift monitoring systems and processes
The following are some of the systems and processes you can install in your forklifts to ensure safe practices in your business.
Sequential seat belts
Most models of forklifts come fitted with sequential seat belts that prevent the forklift from starting up or operating until the driver’s seat belt is fastened. Sequential seat belts have proven to reduce the likelihood of injuries and increase drivers’ chance of survival. Even if sequential seat belts are fitted, there’s still some encouragement needed for drivers to use them, so it’s important that drivers are also trained on the safety benefits.
License data recognition
The best monitoring system will contain license data for each driver and won’t allow a driver to use the forklift if their license has expired. These systems will include the pre-start-up checklist to be completed before machine use. They can also report metered hours, such as lift and seat hours, to give a better indication of how often the forklifts are being used.
Intelligent forklift monitoring systems
Monitoring systems can measure temperature, travel time, fluid pressure and other parameters that drivers can see on their screen. From this, drivers are able to notice any unusual changes to the forklift data that may indicate an upcoming service or repair requirement.
Forklift usage reporting data can also be exported to assist with scheduling forklift maintenance, billing for forklift and driver jobs, and payroll. Some forklift breakdowns are caused by battery failures, so having a battery monitoring system installed in your forklift can prevent this as it provides data on battery usage.
Tracking systems installed in forklifts (such as GPS) help drivers, warehouse managers and supervisors with equipment location. Location tracking can make drivers more accountable for their work since they know their driving habits are being monitored, saving time and increasing productivity as a result.
Data from the monitoring systems showing the forklift usage, location, driver details can provide clarity on responsible parties should an incident occur, and can identify areas that need further training to ensure they reduce the risk of it happening again.
Keeping forklifts visible
Visibility of what’s around you when operating a forklift will prevent injuries from occurring in the work area. However, when drivers have to lift loads more than six metres in height, there’s not much they can see from their seats. This risks goods falling and endangering the driver and other people around. Installing a camera on the forklifts will give drivers a clear view of their load and racking. This will help them to know the exact positioning of their tyres when lifting and storing goods, ensuring that goods are stored safely. Reversing cameras are also available for increased visibility, particularly for crowded warehouses.
Laser level systems can be installed in place of cameras, as the laser beam unit can be placed on top of forklift tyres, just like cameras. A laser line will appear from the beam and onto surfaces so drivers know where the tyres are positioned. This gives drivers more control in handling products and creates a safer working environment, knowing that loads are placed correctly and won’t fall onto the driver or pedestrians.
Forklift warning devices
Warning devices such as flashing or strobe lights are a great feature to notify of forklift presence. Most forklifts are fitted with standard safety lights, and you can enhance visibility by adding a blue strobe light. Blue strobe lights are great for warning pedestrians of an oncoming forklift, especially when they’re in a blind spot or entering an aisle or storage container. A blue spot can be placed on the ground three metres behind a unit to warn other people that a forklift is present. On each side of the forklift, light exclusion zones can be emitted to warn others of the proximity of the forklift, further reducing workplace injuries.
Keeping your employees and visitors forklift-safe
Safety and monitoring systems are designed to create a safer workspace, with the data from these systems enabling managers and supervisors to measure KPI’s and track safety.
Lencrow Forklifts have more than 40 years experience with forklift hire, sales and repairs, and have worked with many of these systems. Contact Lencrow Forklifts on 1300 536 246 for all your forklift needs.