Ross Grassick
Forklift Safety
How to Encourage Active Risk Assessment When It Comes to Forklift Operation
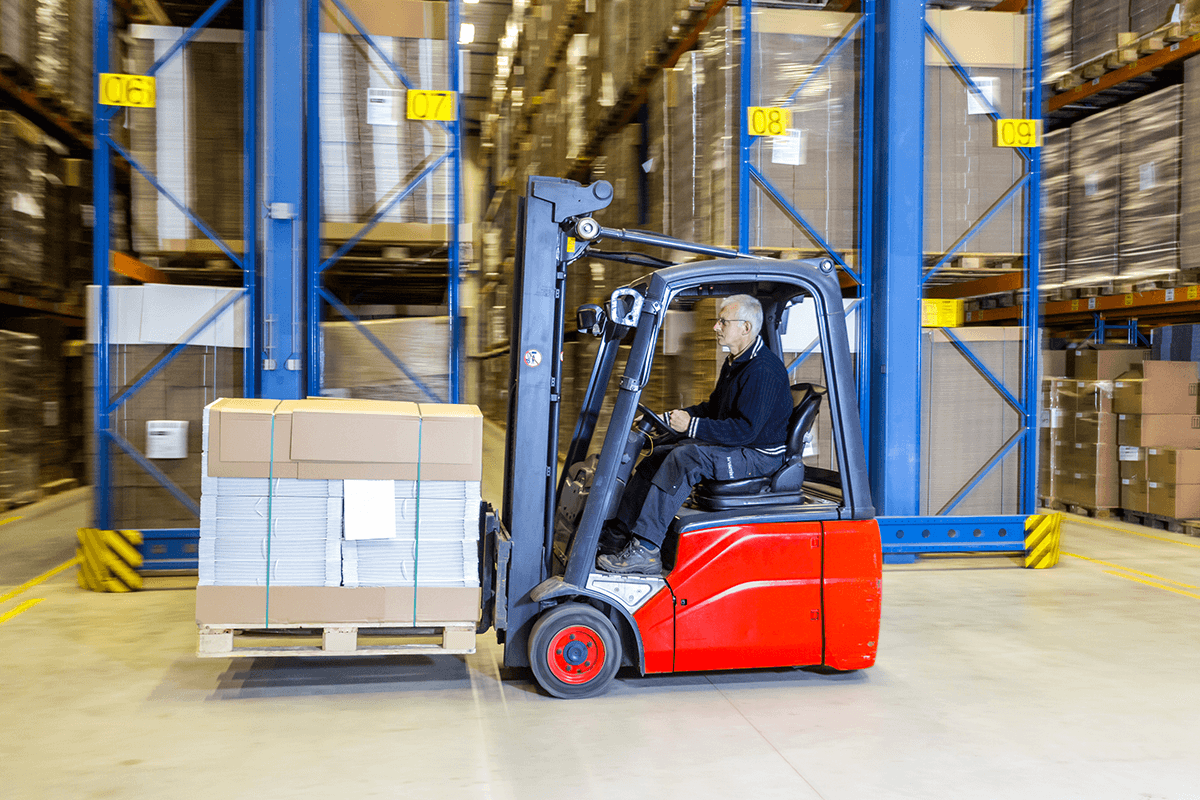
Forklifts are a heavy and dangerous piece of machinery that are used in warehouses, shipping yards and factories to transfer, stack, and lift loads. Even at low speeds, they are one of the common causes of workplace injuries and deaths across Australia. They cannot only involve the driver, but pedestrians as well.
Such incidents can be prevented by knowing how to identify, assess and minimise risk. Businesses must work with their employees to identify and improve work safety outcomes.
Don’t wait until it’s too late. The guide below will show you what to do.
Your responsibilities
As a business owner or workshop manager, you are responsible for creating a safe work environment and safe working systems, as well as providing well maintained and safe machinery, up to date information, training and supervision for all employees.
You will need ensure the necessary safety practices, such as observing speed limits and warning signs, wearing correctly fitted seat belts, slowing down, using alerting sounds such as reversing alarms and horns, are all adhered to to ensure a safe working environment. To find out if you have these in place or if you need implement them, you need to conduct a risk assessment.
Doing risk assessments will help you:
- Identify and control hazards
- Create awareness with employees
- Set the risk management stands according to legal requirements
- Minimise workplace incidents
- Save costs
You must create awareness of the risk assessment plan, as they highlight risks that need to be focused on and open up conversations with those who may be affected.
So, how do risk assessments work?
Identifying hazards
You need to see how people can be injured. You can find this out by inspecting your workplace and looking out for potential situations that might cause an incident. Talk to your employees. Employees should already be reporting any potential hazards they see, but some things may be overlooked, and you’d rather be safe than sorry. This gets everyone involved and further increases awareness.
Aside from immediate incidents, think about it long term. Could there be a potential incident in the near future? Incidents such as high noise pollution could cause hearing loss for your employees if not minimised to a safe level. Ensure that employees are wearing the correct safety gear (such as ear muffs) in noise pollution areas.
Acknowledging people at risk
After you have identified the workplace hazards, you need to then identify who may be at risk and how they may be affected. For example, risks can include:
Forklift instability
The biggest danger associated with a forklift is tipping over. Seatbelts save lives and must be worn at all times to prevent the driver from jumping out and causing themselves further injuries. Tipping over can also injure pedestrians who may be nearby and who might be struck with debris. Forklifts can tip over if you:
- Reverse too quickly
- Brake too quickly
- Accelerate or brake turning a corner
- Accelerate or brake down a slope
- Collide with another vehicle
- Carry an unevenly balanced load
- Drive with forklift arms too high with or without a load.
Operator sprains and strains
Drivers can get long term health problems from sprains and strains in their neck, back, and arms. The common hazards that cause this include:
- Hitting bumps repeatedly or driving on uneven surfaces
- Repeatedly looking up when stacking high
- Repeatedly looking behind while reversing.
Overall, you need to identify which groups may be harmed as they have different requirements. Groups include but are not limited to young workers, disabled workers, migrant workers and groups that may not always be onsite such as visitors, contractors and cleaners.
Evaluate & decide
After you have identified the risks and know who they affect, you must evaluate the risk to decide on which precautions to take. It’s one thing to identify risks, but not taking action does not prevent or minimise the risk.
You need to look at what actions you currently take at your workplace and compare them to good practices. This will allow you to see if you could be doing more to increase the standard in the workplace.
Recording a risk assessment
Failure to implement the necessary precautions can be costly if an incident occurs. Having a written record of your findings is a tangible record that can be used as a reference for future improvements and assessments.
Be sure to have an action plan for the implementation stage. This will allow you to prioritize which risks to action first, and then work your way through efficiently.
Have a traffic management plan
The aim of the traffic management plan is to separate pedestrians and forklifts to ensure the safest movement of traffic in the workplace to minimise collisions. To create your plan, consult with your employees and follow the risk assessment procedures:
Identify the hazard
Study your workplace to identify areas where potential collisions may occur. Ask your employees if they have noticed any problems while driving the forklift and review your incident reports.
Evaluate the risk
The risks are caused by the hazards identified. You need to assess:
- Severity of possible injuries
- Worst damage caused to someone’s health
- If it can happen at any time or if it would be a rare event
- How many people and how frequently employees are exposed to the hazard
Control the risk
Eliminating the risk is most effective way to control them. It if it not possible to eliminate the risk, you will need to consider other ways you can minimise the risk. You may have to:
- Implement speed limiting devices on forklifts
- Provide employee training
- Install warning signs
- Provide an overhead pedestrian walkway
- Remove the forklift completely (eliminating the risk)
Review control measures
Reviewing your control measures ensures that your measures have been implemented and that new hazards haven’t arisen as a result. Whenever there is a near miss, incident, or even changes to your workplace, it is in your best interests that you repeat the hazard management process.
Lencrow Forklifts have more than 40 years’ experience in the materials handling industry, from selling to renting forklifts. For any queries relating to forklift risk assessment, speak to one our experienced staff on 1300 516 431.