Ross Grassick
Forklift Service & Maintenance
Regular Forklift Servicing: Planned Preventative Maintenance Programs
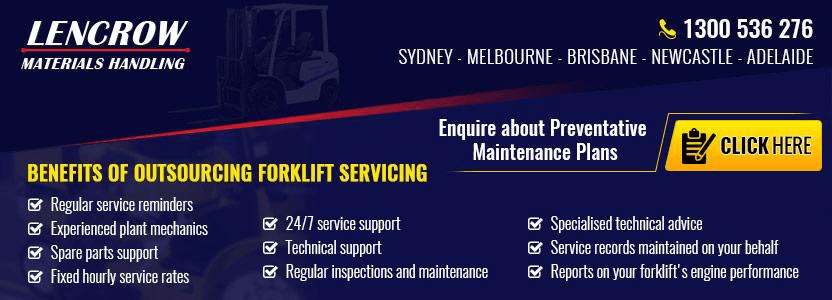
If your operation uses materials handling equipment you should have a regular maintenance plan in place. Service schedules are predetermined by forklift manufacturers and calculated based on hours of operation or by a calendar month, whichever comes first.
Regular forklift maintenance reduces the likelihood experiencing larger, costlier mechanical faults and and forklift repairs. Reduce the risk of accidents, injury or death by ensuring your forklift is in good working order and safe to operate
When you purchase materials handling equipment, whether its new or used equipment, find out about the manufacturers recommendations, which are located in forklift operators manual. If you have purchased a second hand forklift always request a record of the service history – reputable suppliers or well-maintained privately owned forklifts will be able provide a full service history.
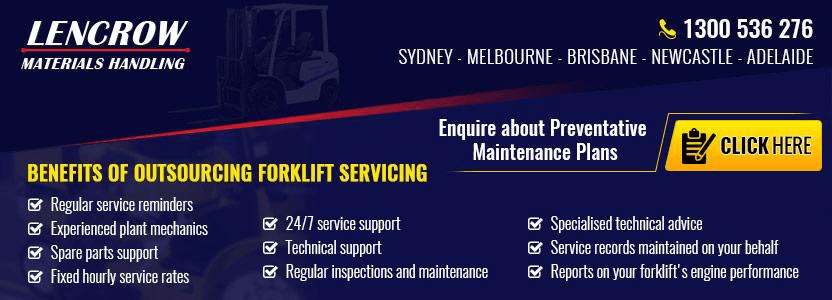
If you are a business owner, forklift owner or operator you can find forklift service providers who will manage your maintenance schedule for you – we like to call this your Planned Preventative Maintenance. The benefits of outsourcing forklift servicing include;
- Regular service reminders
- Qualified and experienced plant mechanics
- Spare parts support
- Fixed hourly service rates
- Reduced likelihood of major faults
- 24/7 service support
- Technical support in the event of a breakdown
- Safer forklifts for your operation with regular inspections and maintenance
- Access to specialised technical advice and other forklift services
- Service records maintained on your behalf
- Regular reports on your forklift’s engine performance
- Support customised to how your operation utilises the forklift fleet
- Transparent service and repair quotations
Reputable forklift suppliers will customise a maintenance plan specific to the make and model of your forklift or the entire fleet. If your business productivity is reliant on functional equipment look for a supplier with fast response times, access to a large network of field service mechanics and vehicles. Forklift Field service networks are capable of fulfilling standard services on site and have a range of tools and equipment in their vehicles.
When you begin looking for a forklift maintenance plan and contact a supplier, the Customer Relationship Manager should contact you and arrange an appointment on your site. Customer Relationship Manager’s usually come from a technical background and are qualified to tailor services schedules based on experienced knowledge and training.
During this first appointment the Customer Relationship Manager will:
- Note the make, model and serial number/s of your forklift/s
- Visually inspect the existing condition of the forklift/s
- Test the forklifts drive and mast functions
- Ask if you need it serviced or have identified specific faults or an irregularity
- Request information about the known service history
- Provide information about their company’s standard service inclusions
Other information that should be discussed in the initial consultation include:
- Who the primary site contact is for each scheduled service
- Preferred method of contact for when services are due (email, text, call)
- Site inductions that may be required for your site
- PPE requirements for field technicians (witches hats, ear protection, hard hat, etc.)
After the initial inspection, the Customer Relationship Manager will present a recommendation for your fleets Planned Preventative Maintenance Program. It’s important to choose a forklift service that offer a fixed price for labour and set regular service checklists. Service and repair quotes should be transparent and approved by you prior to any work being commenced.
As the hours increase on your forklift the standard service might change slightly as per the manufacturers specifications. For example; at 1000 hours filters may need to be changed instead of visually inspected. Ask about this when you review your customised maintenance plan.
Lencrow Materials Handling use a 22 point checklist for every scheduled service. Our technicians complete the checklist on every visit and provide you with a report on the service outcomes. Our service vehicles have state of the art computer technology installed that allows us to keep your forklift/s records up to date. These records allow us to generate reports about your forklifts engine performance, hours of operation, fleet productivity and other useful reports that help you to maximise your operation’s handling.
Download our Preventative Maintenance Plan fact sheet and compare it with other companies. Our Planned Preventative Maintenance Program provides you with the certainty that each component will be inspected every time your due for a scheduled service and quick response times in the event of a breakdown. Our field service network services the east coast of Australia and South Australia. Lencrow’s team of forklift mechanics are qualified and experienced in providing full technical support across a wide range of forklift makes and models.